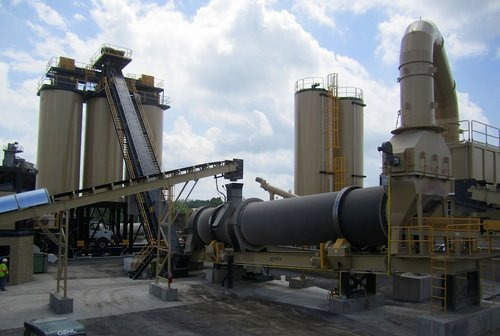
Producing hot mix asphalt concrete is an energy intensive process involving heating aggregate up to 435 degrees F, then mixing in asphalt cement and recycled materials. Typical recyclables are asphalt concrete removed from older pavements & garbage, asphalt shingles, plastic and glass.
So, the plant site shown has a stockpile of aggregate that is fed via belts into the right side of the plant. The dark gray barrel, or drum, is where the aggregate is heated. The drum is usually heated by natural gas burners. This is a continuous mixing plant. The HMAC components are continuously moving through the drum. The liquid asphalt cement, stored in the two silos at the picture’s center background, is added at about the bottom third of the drum. Also added is recycled material from the conveyor belt to the left. Mixing is completed by the time the mixture moves towards the drum’s end where a second conveyor belt carries the mixture to storage silos. Trucks will drive under the silos to receive a load of hot mix asphalt concrete.
The silos are necessary to store enough HMAC for the day’s need. A silo usually holds 350 to 400 tons of HMAC and a truck will carry 15 to 25 tons. A plant operator will start a plant up at 3 or 4 am to build up full silos for the day.
Photograph from ALmix – Asphalt Equipment Company website